In the medical device industry, Design for Manufacturability (DFM) is an important practice that tries to make products that are easier, cheaper, and more efficient to make. As the need for safe, effective, and high-quality medical devices grows, DFM has become an important part of the product development lifecycle. Using DFM strategies early in the design phase not only helps make manufacturing processes better, but it also makes sure that they follow the rules, lowers production costs, and speeds up the time it takes to get the product to market.
In this article, we’ll look at the best ways to use Design for Manufacturability in medical devices and how it can make the manufacturing process better.
- Simplify the Design
One of the main ideas behind DFM is to make the product design simpler. When designs are too complicated, it can be hard to make them. This can mean higher costs, longer production times, and mistakes that could happen during the manufacturing process. By focusing on simplicity, designers can get rid of parts or features that don’t add anything useful to the device’s function.
Best Practice:
Reduce the number of parts: Fewer parts mean fewer steps to put them together, which lowers the chance of mistakes and speeds up the process.
Think about making things the same: Use standard parts or components whenever you can. This lowers the cost of buying things and lowers the chance of mistakes being made during production.
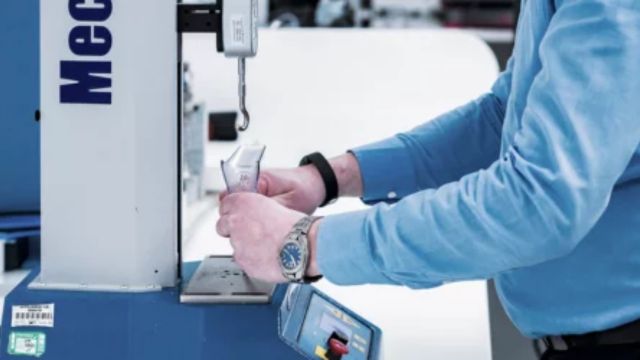
- Design for Assembly (DFA)
Design for Assembly (DFA) is a principle that is very similar to DFM. It focuses on making medical devices in a way that makes the process of putting them together faster and cheaper. The more simple it is to put together a product, the faster and cheaper it will be to make it.
Ease of Assembly: Design parts that are easy to align, snap together, or require minimal handling during assembly.
Best Practice:
Easy to put together: Make parts that are easy to line up, snap together, or don’t need much handling during assembly.
- Consider Material Selection Carefully
Choosing the right materials is one of the most important parts of the DFM process for medical devices. The right materials not only make the device work and keep it safe, but they also have a big impact on how it is made. Using materials that are hard to work with or cost a lot to get can make production take longer and cost more.
Best Practice:
Choose materials that are easy to work with. For instance, thermoplastics and metals that are easy to find and shape, weld, or machine can make the manufacturing process go more smoothly.
Material compatibility: Make sure that the material you choose works well with the other materials used in the device so you don’t have to do expensive rework during assembly.
- Design for Regulatory Compliance
The FDA and ISO have strict rules that medical devices must follow. Adding these compliance requirements early in the design process helps make sure that the product can pass inspection by regulators without expensive delays.
Best Practice:
Design with quality in mind: Include design elements that help the device meet safety standards, such as proper labelling, safety features, and biocompatibility standards.
Documentation: Keep detailed notes on the choices you make about design, the materials you use, and the tests you run. This can help speed up the process of getting regulatory approval and stop delays.
- Design for Testing and Validation
Testing and validation are very important steps in making medical devices because they make sure the product meets safety and performance standards. Designing for testing means making products that are easier to test and validate while they are being made. This helps find problems before they happen.
Best Practice:
Built-in test points: Make the product so that it can be tested easily, like by including testing ports that are easy to get to or sensors that give real-time feedback.
Prototype and iterate: Early prototypes let designers test the design in a real-world setting, which helps them find any problems before full-scale production.
- Collaborate with Manufacturing Teams Early
important for design and manufacturing teams to work together early on. Engineers and designers should work together early on in the development process to make sure that the design is as good as it can be for manufacturing.
Best Practice:
Regular design reviews: Hold regular meetings between the design and manufacturing teams to discuss potential challenges and improvements.
Incorporate feedback: Manufacturing teams often have valuable insights on the feasibility of certain designs and processes, so incorporating their feedback is key to improving manufacturability.
- Use of Advanced Technologies
The adoption of advanced manufacturing technologies, such as automation, 3D printing, and robotics, can greatly enhance the efficiency and precision of medical device production. These technologies can reduce human error, improve the consistency of manufacturing, and streamline production processes.
Best Practice:
Incorporate automation: Automated assembly lines or robotics can help reduce labor costs, improve precision, and speed up production.
Utilize 3D printing for prototyping: Rapid prototyping using 3D printing enables designers to test and iterate their designs quickly, reducing time and costs before full-scale production.
Conclusion
To make medical devices successfully, it is important to use Design for Manufacturability (DFM). Companies can lower production costs, speed up time to market, and raise the overall quality of their products by making designs simpler, choosing materials carefully, focussing on following the rules, and working with manufacturing teams early on.
Using DFM principles not only makes the manufacturing process better, but it also makes sure that medical devices are safe, effective, and of high quality, which is what the healthcare industry needs more of.
At J & J Supplies, we know how important it is to improve manufacturing processes to make sure that medical devices and supplies meet the highest quality standards. Keep up with the newest developments in medical supply and clinical engineering. Sign up for our newsletter to get regular updates on the latest news, best practices, and expert opinions in your field.
FAQ
What is the main goal of Design for Manufacturability (DFM)?What is the main goal of Design for Manufacturability (DFM)?
The main goal of DFM is to simplify the design process, reduce production costs, minimize errors, and accelerate the time to market by ensuring that the product is easy and cost-effective to manufacture.
How does Design for Manufacturability impact the medical device industry?
DFM helps manufacturers streamline their production processes, ensure regulatory compliance, reduce material and labor costs, and improve product quality, which is crucial in the highly regulated medical device industry.
What role does material selection play in DFM for medical devices?
Material selection is critical in DFM as it impacts the manufacturability of the device, production costs, and the overall performance and safety of the medical device.