The idea of a Digital Twin has become one of the most talked-about new technologies in the world of medical production in the last few years. A Digital Twin is like a virtual model that shows how genuine systems, processes, or surroundings work in real time. This computerized model makes it possible to fully watch, study, and improve production processes. The idea of making a Digital Twin for medical production has completely changed the game. It has brought huge benefits by making things more efficient, improving product quality, and making things safer. But putting a Digital Twin to use in the medical manufacturing industry does come with its own set of problems.
What does “Digital Twin” mean?
A digital twin is a digital copy of a real object, process, or system that can change and be used for simulation and analysis. This technology combines data that is acquired in real time by sensors that are built into physical equipment, gadgets, and manufacturing processes. A Digital Twin could stand for the whole facility, the production line, or even just one medical device in medical manufacturing.
Advantages of Using a Digital Twin in Medical Manufacturing
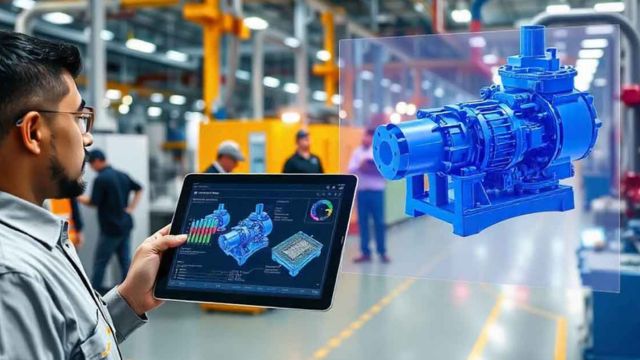
Improved Efficiency in Operations
One of the best things about using a Digital Twin in medical manufacturing is that it may make operations run more smoothly. Manufacturers can test and simulate different situations without compromising real-world operations by making a virtual model of the whole manufacturing system. This lets producers make decisions based on data to make manufacturing more efficient, cut down on waste, and use resources better.
Maintenance that is based on predictions
To make sure that medical equipment fulfills regulatory criteria and keeps working properly, maintenance is very important. By keeping an eye on how machines work and finding problems before they happen, a Digital Twin can help with predictive maintenance. This proactive strategy lowers unplanned downtime, extends the life of equipment, and makes manufacturing operations more reliable overall.
Better quality of the product
Quality control is very important in the medical manufacturing industry. The Digital Twin can help keep an eye on the production process all the time and compare it to the best performance indicators. Manufacturers can take steps to fix problems early in the process to make sure the items they make are safe and of high quality. This means fewer flaws, fewer recalls, and more reliable products.
Following the rules
One of the most regulated sectors in the world is making medical devices. It can be hard to make sure that you follow standards like FDA, ISO, and CE. With a Digital Twin, producers can readily see in real time whether their processes are following the rules of the industry. This makes sure that all procedures are in line with the rules. The system can also be used to keep detailed records for audits, which makes the process of keeping records faster and easier.
Faster Time to Market
The capacity to test and simulate alternative manufacturing processes in a virtual environment cuts down on the time it takes to get a product to market. Manufacturers may quickly make changes and improvements by finding problems and testing product designs and procedures in a virtual area. In the end, this speeds up the process of making things and getting innovative medical gadgets to market faster.
Monitoring in real time
A Digital Twin lets you keep an eye on every part of the production process in real time. Manufacturers can obtain a rapid picture of any problems or strange things that may happen, from how well machines work to how much material they use. This real-time information lets them fix problems before they get worse, which keeps things running smoothly and effectively.
Problems with making a digital twin in medical manufacturing
There are a lot of good things about using a Digital Twin in medical manufacturing, but there are also a lot of problems that producers need to think about:
A lot of money up front
The cost of setting up a Digital Twin can be high, especially for businesses that are new to the technology. The method includes not only connecting IoT devices and smart sensors but also making the virtual model, which needs specialist software and knowledge. Small and medium-sized businesses may have trouble justifying the initial investment, even if the long-term advantages usually outweigh the expenses.
Worries about data security and privacy
There are possible security vulnerabilities when sensors and other connected devices collect and analyze real-time data. Medical manufacturing contains private information, thus it’s very important to protect patient data and intellectual property. To protect data and follow data privacy laws, manufacturers must put in place effective cybersecurity safeguards.
How hard it is to integrate
To make a Digital Twin, you need to connect several systems, sensors, and devices across the whole production process. This can be hard and take a lot of effort and knowledge. It may be necessary to upgrade or replace legacy systems that don’t work with the new technology, which makes the integration more expensive and difficult.
Requirements for Training and Skills
To set up a Digital Twin, you need skilled workers who can read the data, run simulations, and make the manufacturing process better. It’s important to train personnel on how to use and administer the new system. In some circumstances, firms may need to retain experts to oversee the adoption and management of Digital Twin technology.
Regular Upkeep
After a Digital Twin is set up, it needs to be updated and maintained on a regular basis to make sure it works and is accurate. To stay useful, the system has to get real-time data all the time. This means that manufacturers need to have a strong plan for managing and maintaining data to make sure the system keeps working well.
Conclusion
Making a Digital Twin for medical production can be very helpful in many ways, such as making operations run more smoothly, allowing for predictive maintenance, improving product quality, and making sure that the company follows industry rules. Companies also need to be mindful of the problems, such as high initial costs, worries about data security, and the difficulty of integrating new systems. Manufacturers can use Digital Twin technology to change the way they do business and stay ahead in a market that is becoming more competitive by carefully planning the deployment and making sure they have the proper resources in place.
We at J & J Supplies stay up to current on the newest developments in medical and clinical engineering so that we can give you the most up-to-date information and news. Keep up with new technology, trends, and ideas in your field. Sign up for our newsletter to have the latest news and updates sent straight to your inbox. Come with us as we keep helping the medical manufacturing community!
Frequently Asked Questions (FAQ)
Yes, the initial setup cost can be high due to the need for advanced sensors, software, and expertise. However, the long-term benefits typically outweigh the costs.What is a Digital Twin in medical manufacturing?
A Digital Twin is a virtual model of a physical system or process in medical manufacturing, used for simulation, monitoring, and optimization of operations.
What are the benefits of using a Digital Twin in medical manufacturing?
Benefits include improved operational efficiency, predictive maintenance, enhanced product quality, regulatory compliance, and faster time-to-market for products.
What challenges are associated with creating a Digital Twin in medical manufacturing?
The main challenges include high initial investment, data security concerns, integration complexity, skill requirements, and ongoing maintenance needs.
How can Digital Twin technology help in ensuring regulatory compliance?
Digital Twin technology allows for real-time monitoring and tracking of compliance with regulations such as FDA, ISO, and CE standards, ensuring all processes adhere to industry guidelines.
Is it expensive to implement a Digital Twin in medical manufacturing?
Yes, the initial setup cost can be high due to the need for advanced sensors, software, and expertise. However, the long-term benefits typically outweigh the costs.