In recent years, the integration of Digital Twin technology has become a revolutionary force in various industries, and the medical manufacturing sector is no exception. A Digital Twin refers to the digital replica of a physical object, system, or process, allowing for real-time monitoring, analysis, and optimization. By simulating real-world conditions, this technology offers manufacturers the ability to improve efficiency, reduce costs, and enhance product quality.
In medical manufacturing, the importance of creating a Digital Twin cannot be overstated. With the increasing complexity of medical devices and the rigorous regulatory requirements in the industry, leveraging a digital twin for medical device manufacturing provides manufacturers with a competitive edge. However, like any innovative technology, it comes with its own set of challenges.
Benefits of Creating a Digital Twin in Medical Manufacturing
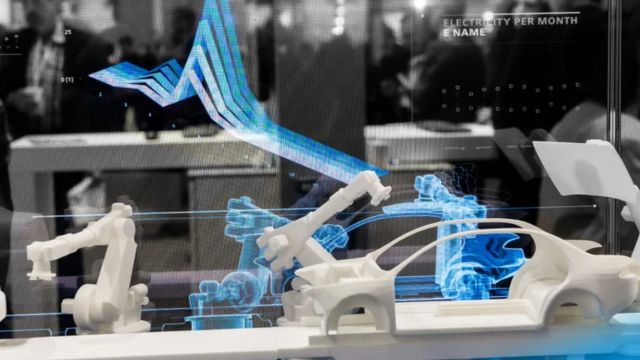
Enhanced Design and Prototyping:
One of the most significant advantages of Digital Twin technology in medical manufacturing is its impact on the design and prototyping phase. Manufacturers can create virtual models of their medical devices, allowing them to test and modify designs digitally before moving to the physical production process. This helps in identifying flaws and inefficiencies early, minimizing costly changes and delays later in the process.
Predictive Maintenance and Monitoring:
By continuously monitoring the performance of medical devices throughout their lifecycle, Digital Twins help in detecting potential failures before they occur. In medical manufacturing, this predictive maintenance is invaluable as it ensures devices function optimally, thereby reducing the risk of malfunctions. This aspect is crucial in maintaining patient safety, especially for devices used in critical care or high-risk environments.
Improved Supply Chain Management:
Digital Twins allow manufacturers to track the entire supply chain in real-time. From the sourcing of raw materials to the delivery of finished products, manufacturers can optimize each step of the process. By simulating various scenarios and outcomes, manufacturers can improve lead times, reduce stockouts, and better manage inventory, ultimately enhancing the efficiency and reliability of the supply chain.
Regulatory Compliance and Documentation:
The medical device industry is heavily regulated, with stringent requirements for product safety and quality. A Digital Twin allows for continuous tracking and documentation of product quality, ensuring compliance with industry standards such as ISO 13485 and FDA regulations. By providing accurate data on product performance and maintenance, it also helps streamline the audit process and ensures smoother interactions with regulatory bodies.
Cost Reduction:
Manufacturing and maintaining physical prototypes is expensive, especially when mistakes are made. With Digital Twin technology, manufacturers can conduct simulations to identify potential issues before they manifest in the real world, significantly reducing the cost of rework, repairs, and scrap materials. Moreover, the insights gained from digital modeling can help optimize production processes, reducing waste and improving overall resource utilization.
Real-time Collaboration:
Digital Twin technology allows for greater collaboration across departments and even with external stakeholders. Engineers, designers, and technicians can all access the same virtual models, making it easier to work together in real-time, irrespective of location. This enhances productivity and fosters innovation, as teams can rapidly iterate and test new ideas.
Challenges of Creating a Digital Twin in Medical Manufacturing
Data Complexity and Integration:
While Digital Twin technology can offer significant benefits, its implementation requires the integration of vast amounts of data from various sources, such as sensors, equipment, and production systems. Managing this data can be overwhelming, especially if the existing infrastructure is not equipped to handle such complexity. Moreover, integrating legacy systems with new technologies can be a challenge, requiring significant investment in both time and resources.
High Initial Investment:
Developing and implementing a Digital Twin system requires a substantial initial investment in technology, including software, hardware, and training. The costs associated with setting up the required infrastructure can be prohibitive for smaller manufacturers or those with limited resources. However, the long-term benefits of improved efficiency and cost savings can often justify the upfront expenditure.
Security and Privacy Concerns:
Digital Twins involve the continuous transfer of data between physical devices and their digital counterparts. This makes them vulnerable to cyber threats and breaches. In the medical manufacturing industry, where product safety and data privacy are paramount, ensuring the security of Digital Twin systems is critical. Manufacturers must implement robust cybersecurity measures to protect sensitive information and prevent unauthorized access.
Skillset and Training:
The implementation of Digital Twin technology requires a workforce with specialized skills, including expertise in data analysis, simulation, and advanced engineering. Manufacturers may face challenges in finding and training the right talent to manage and operate Digital Twin systems. Additionally, employees must be continuously updated on the evolving technology to ensure they are leveraging its full potential.
Real-time Data Accuracy:
The accuracy of the data fed into the Digital Twin is paramount for its effectiveness. Any inaccuracies in the real-time data collected from sensors or production lines can lead to flawed simulations, resulting in poor decision-making. Ensuring the consistency and reliability of data sources is essential to maintaining the credibility of the digital model.
Conclusion:
In summary, Digital Twin technology has the potential to revolutionize medical manufacturing by providing real-time insights, reducing costs, and ensuring product quality and compliance. The benefits are clear: enhanced design, predictive maintenance, optimized supply chains, and better regulatory adherence. However, the challenges — including data complexity, high initial costs, security concerns, and the need for specialized skills — should not be underestimated.
By carefully addressing these challenges and investing in the right technologies, medical manufacturers can leverage Digital Twin technology to improve efficiency, innovate, and stay competitive in an increasingly complex industry.
Stay ahead in the medical manufacturing industry by keeping up with the latest trends and innovations! Subscribe to our website for expert insights on medical supplies, clinical engineering, and manufacturing best practices. Get the latest updates on cutting-edge technologies and industry standards that will help your business thrive.
FAQs
What is a Digital Twin in medical manufacturing?
A Digital Twin in medical manufacturing is a virtual representation of a physical medical device or manufacturing process. It allows for real-time monitoring, data analysis, and optimization to improve product design, production efficiency, and quality.
What are the main benefits of using Digital Twin technology in medical manufacturing?
The key benefits include enhanced design and prototyping, predictive maintenance, improved supply chain management, regulatory compliance, cost reduction, and real-time collaboration across teams.
What challenges are associated with Digital Twin technology in medical manufacturing?
Challenges include data complexity, high initial investment costs, security concerns, the need for specialized skills, and ensuring the accuracy of real-time data.
How does Digital Twin technology help with regulatory compliance?
Digital Twin technology helps maintain detailed records of product performance and maintenance, ensuring compliance with industry standards such as ISO 13485 and FDA regulations.
Is Digital Twin technology suitable for small medical manufacturers?
While the initial investment can be high, the long-term benefits of improved efficiency and cost savings often outweigh the costs, making Digital Twin technology a worthwhile investment for manufacturers of all sizes.