In the highly competitive medical device manufacturing industry, reducing lead times is crucial for staying ahead. The faster you can bring your products to market, the more competitive advantage you gain. However, cutting lead times isn’t just about speeding up production—it’s about optimizing processes, improving communication, and leveraging technology effectively. In this article, we’ll explore the best strategies to reduce lead times in medical device production and improve operational efficiency.
What Are Lead Times in Medical Device Production?
Lead time refers to the time it takes to complete a process, from the receipt of raw materials or orders to the delivery of finished products. In medical device manufacturing, reducing lead times involves minimizing the time spent on each step of production, from design and prototyping to testing, assembly, and packaging. Shorter lead times not only improve supply chain efficiency but also reduce costs, improve customer satisfaction, and allow businesses to respond more quickly to market demands.
Best Strategies for Reducing Lead Times in Medical Device Production
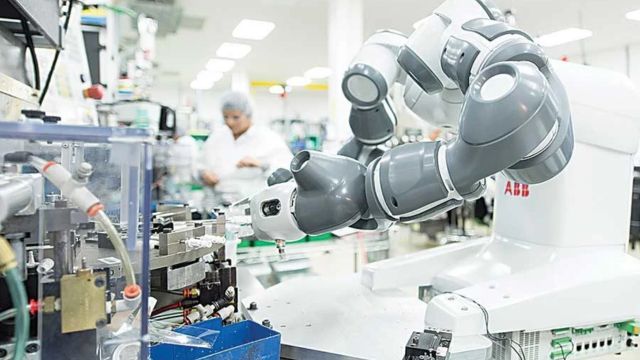
- Implement Lean Manufacturing Techniques
One of the most effective strategies for reducing lead times is the implementation of lean manufacturing. Lean principles focus on eliminating waste in all areas of production, including overproduction, excess inventory, long waiting times, and unnecessary motion. By identifying and eliminating inefficiencies, manufacturers can reduce cycle times and speed up production.
- Value Stream Mapping (VSM) can help identify bottlenecks and waste in the production process, enabling targeted improvements.
- Just-in-Time (JIT) inventory management ensures that materials are available when needed, reducing waiting times and the need for excess stock.
- Kaizen (continuous improvement) promotes small, incremental changes to processes, encouraging ongoing efficiency gains.
By applying these principles, medical device manufacturers can streamline production and cut down lead times without compromising quality.
- Invest in Automation and Robotics
Automation and robotics are transforming the medical device manufacturing industry. Automated systems can perform repetitive tasks much faster and more accurately than human workers, reducing errors and cycle times.
- Robotic Process Automation (RPA) can handle tasks such as assembly, packaging, and inspection, speeding up production and minimizing human error.
- Automated testing equipment ensures faster and more reliable product testing, reducing downtime between stages of production.
By automating critical processes, manufacturers can not only reduce lead times but also increase precision and reduce the risk of defects.
- Optimize Supply Chain Management
The supply chain plays a crucial role in lead times. Delays in procuring materials or shipping finished goods can severely impact production schedules. Effective supply chain management (SCM) is essential to ensure a smooth flow of materials and reduce lead times.
- Supplier relationship management (SRM): By building strong relationships with reliable suppliers, manufacturers can secure faster deliveries of materials and ensure the quality of components.
- Inventory optimization: By using advanced demand forecasting techniques, manufacturers can better predict the materials they need, reducing stock-outs and delays.
- Nearshoring: Instead of relying on distant suppliers, some manufacturers opt to work with local suppliers to reduce transportation time and costs.
Efficient supply chain management helps medical device manufacturers mitigate delays, keep inventory levels in check, and speed up production.
- Utilize Advanced Manufacturing Technologies
Incorporating cutting-edge manufacturing technologies can drastically reduce lead times by improving production speed and precision. Technologies like 3D printing and Additive Manufacturing (AM) allow for rapid prototyping and direct manufacturing of medical devices.
- 3D Printing: 3D printing can shorten the prototyping phase significantly. Manufacturers can create prototypes in hours rather than days or weeks, enabling faster design iterations and faster time-to-market.
- CNC Machining: For precision manufacturing, Computer Numerical Control (CNC) machines can reduce the need for manual labor, improving production speed and consistency.
By leveraging these technologies, manufacturers can reduce delays during the design and prototyping stages, which in turn reduces overall lead times.
- Improve Cross-Functional Collaboration
Reducing lead times isn’t only about optimizing the production floor. Improving communication and collaboration between different departments is equally important. If design, engineering, production, and quality control teams work in silos, delays can occur at every stage of production.
- Cross-functional teams can identify and resolve issues quickly, ensuring that changes are implemented without unnecessary delays.
- Project management tools such as Kanban or Agile frameworks can help teams stay aligned and track progress in real time, ensuring that all stakeholders are on the same page.
By fostering a culture of collaboration and using modern project management tools, manufacturers can streamline communication and avoid delays between departments.
- Prioritize Product Standardization
Standardizing components and processes can lead to significant reductions in lead times. When products are built using standardized parts and modular designs, it becomes easier to maintain a consistent workflow. Standardization also reduces the need for customized production runs, which are often more time-consuming.
Modular design allows manufacturers to quickly assemble medical devices by combining standardized components, rather than building each product from scratch.
Component sourcing: By using standardized components, manufacturers can reduce the procurement time and minimize the risk of delays caused by custom parts.
Standardization helps simplify the production process and reduce lead times, making it easier to manage inventory and production schedules.
Conclusion
Reducing lead times in medical device production is an ongoing process that requires continuous improvement. By adopting lean manufacturing principles, investing in automation, optimizing supply chain management, using advanced technologies, improving cross-functional collaboration, and prioritizing standardization, manufacturers can significantly cut down lead times while maintaining high standards of quality and safety. These strategies help manufacturers meet market demand more quickly and stay competitive in a rapidly evolving industry.
Stay ahead of the curve by keeping your operations efficient and streamlined. At JandJ Supplies, we offer expert insights into the latest in medical supplies, clinical engineering, and manufacturing strategies. Visit our site for more industry news, updates, and best practices to boost your operational efficiency today!
FAQs
How can lean manufacturing techniques specifically reduce lead times in medical device production?
Lean manufacturing focuses on reducing waste and improving efficiency in every step of the production process. By eliminating unnecessary steps, optimizing workflows, and ensuring timely availability of materials, lead times can be significantly reduced.
What role does automation play in speeding up medical device production?
Automation reduces the time spent on manual tasks such as assembly and testing. Robots and automated systems can perform these tasks faster and more accurately, thus reducing production time and minimizing errors.
How does 3D printing reduce lead times in medical device manufacturing?
3D printing allows manufacturers to rapidly prototype and test new designs, which significantly reduces the time required to iterate and finalize designs. This accelerates the product development process and shortens time-to-market.
Can improving supplier relationships really help reduce lead times?
Yes, strong relationships with reliable suppliers ensure that materials are delivered on time and meet quality standards. This reduces delays in the production process and helps keep the manufacturing schedule on track.